Bachelor of Science, Biology
My undergraduate research was on the behavior and genetics of certain ant species.
Ants play critical roles in our environment everywhere in the world:
they eat a wide variety of matter, cycling organic waste back into food for other insects and animals;
they dig tunnels and aerate the soil, paving the way for microorganisms to enrich the land and
make it fertile for all life; they feed on seeds, spreading those around and dispersing plants farther than otherwise possible.
They outnumber us by at least five orders of magnitude, and they can lead complicated and interesting lives.
Acromyrmex versicolor, a species of leafcutter ants (and the specialty of my first research mentor),
grow farms of fungus. They feed the fungus with scraps of fresh leaves and drink the nutritious sap it produces.
These ants don't bite or sting. They can almost seem friendly, mistaking your arm hair for a leaf and trying to give you a trim.
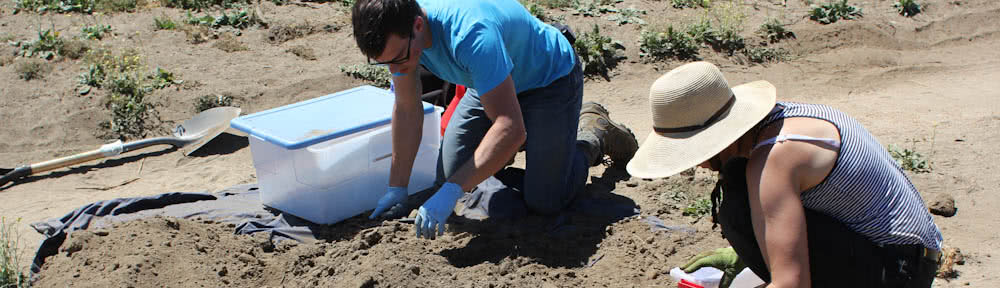
Digging up
Pogonomyrmex ant colonies in the California desert to collect queens and brood from their chambers.
Pogo from the Greek root for
beard and
myrmex from
ant; the name
bearded ant refers to a structure under their mandible that helps them manipulate fine particles.
Some of the students in our lab explored the bacterial populations that may inhabit the ants' beards.
My work was focused on the behavior of their queens when sharing a home and the duties of maintaining it.
Unlike
Acromyrmex, these ants sting with a venom at least twenty times more powerful than that of a honey bee. For one species, only twelve stings can be enough to kill a four pound rat—giving
Pogonomyrmex the most lethal sting of any known ant. The effects of their venom, which include destroying blood cells, are caused by a wide variety of proteins, enzymes, and inflammatory compounds.
The Pogonomyrmex Californicus queens we collected lived in pairs in almost 200 of these nests. The nests allowed us to see the whole colony at once so we could follow its development. We made about 80,000 observations over the course of a week, working in shifts around the clock.
Ant queens don't generally get along, but certain populations of this species can be uniquely cooperative.
Ants in progressive stages of development: eggs, a larva, a pupa, and a brood-tending worker. The brood tenders are generally young and don't leave the nest, to avoid infection.
These brood are being fed grass seeds, which is how species of Pogonomyrmex get the common name seed harvesting ants.
A worker and her queen tending larvae and eggs. Ant workers are always female, and cannot reproduce. The colony does not produce males until their reproductive season.
We marked each queen with model paint to track their individual behavior in groups. The best way I found was to let her bite my thumb and get the paint on while she's distracted, but I think other students had a little more finesse.
Design & Prototyping
My first CAD model
We make a product for the Porsche 911 turbo air inlet that fits a pressure tap via a proprietary connector.
Late 2016, we lost access to the bungs for that connector and had to make new ones.
I spent the day learning how to use
Onshape, a web-based CAD application built on Parasolid, and modeled the bung we needed.
I brought this to our CNC manufacturer and had 100 of them made—and they worked!
I was so excited that I immediately switched to Solidworks and continued learning over the next few years.
The bung screws into a boss on this pressure tube.
Huratron Exhaust
Flynn's Own Lamborghini Huracán
Huratron 2.0 is the second iteration of the owner's extremely bold concept for a future-fantasy supercar. Inspired by the 1982 classic
TRON, the metallic blue wrap and high-specular accents turn this Huracán into a 200mph glowing wireframe in the night.
Scottsdale AZ's
EAWraps set the bar with their flawless vinyl work; so when I teamed up with
Ardent Performance to design the exhaust, I knew we needed something that could stand out from all the flash while fitting perfectly into place.
The geometric concept is directly inspired by the
Vorsteiner valance surrounding the outlets.
Breaking the space up isomorphically evokes fractal geometry tropes from the
virtual world fantasy genre—and the simple geometry alludes to the graphics of the
TRON era.
The thin faces on the exhaust tips extend just to the end of the body, creating another flat geometric element and smoothing the visual flow across the tail.
A mirror polish creates glowing lines that float in the negative space of the bodywork.
I had the good fortune to work alongside the owner of Ardent Performance while he fabricated the exhaust system by hand. Working directly with parts on the car enabled me to get the right fit from first measurements.
The exhaust tips were mounted to the carbon valance, so light weight was key. The exhaust pipes float in the tip with a swaged sleeve.
Bent sheetmetal construction was the obvious choice; despite the high labor cost to fabricate,
the quick turnaround of waterjet-cut parts was crucial for a deadline measured in days.
A self-fixturing design allowed for welding true angles with just a square to set up tacks.
Cast aluminum intercooler end-tanks
Our partners develop turbocharged off-road vehicles with significantly higher intake pressures than what the factory builds in.
With boost comes heat, so they needed a much larger air-to-air intercooler to bring intake temperatures down for efficient combustion.
I was given their chosen intercooler core and asked to make it fit into the stock intake tract.
This was going to be a high-volume product,
so the labor of tube and sheet construction would not be cost effective.
I did try a sheetmetal design, but it was an easy pass.
CNC milling was out of the question as most of the billet would be wasted. They had to be cast, which was new territory for me.
I tried a number of different geometries including differently curved envelopes and, as a marketable feature, flow guides.
My research on sand casting led me to reduce the complexity to keep it within my risk tolerance. I wanted this to turn out right.
For one of the more complicated shapes I commissioned a mockup in FDM glass fiber nylon, as an exercise to explore the material. The part held up to vibration, stress, and heat, but the cost and complexity weren't justified by the gimmick.
Still, I'm impressed how resilient it was for a 3D print—nothing short of a MAP torch could get the material to fail.
I wanted some evidence to choose between a flat or rounded profile for the air-guiding surfaces,
so I built a detailed model in Solidworks and looked at separation and eddies.
Ultimately I concluded that the simulation wouldn't be informative without modeling the pulsed flow in the real engine,
which was outside the scope of this project.
I finalized a design rooted in the style of the seller's other products and we fabricated a sheetmetal prototype.
Performance on the test vehicle was good so we went to casting.
This product went on the market January 2019 and features in race applications.
In the end, this was too complicated to build affordably and we went back to the original design.
The final part can be made from start to finish by any fabrication employee, using only one spot weld.
Dirt bike oil radiator
Prototyped in PLA.
Made from saw cut extrusion, waterjet cut sheet, and turned bungs; all in 6061-T6 and brazed.
Next-Day Drawing and Rapid Prototyping
T4 turbo flange
Branded intake manifold hat
Port injection manifold spacer
Polar coordinate measuring machine
I made this after we had
Hexagon's ROMER arm in the shop to scan the underbody of a car.
I used two belt-reduced encoders for 2 arc minute resolution in azimuth and elevation.
Radius used time-of-flight IR sensing, but accuracy was not acceptable and LIDAR was not cost effective.
Firmware runs on Arduino Uno and points are plotted with OpenGL on Windows.
Nylon washers for low friction
The client communicates with the hardware via USB serial. Made using OpenGL via OpenTK in C#.
PartCenter implements a concept I imagined for my sales team: all of their orders on one page, immediately searchable when the phone rang. Detailed status indicators give them the information they need to respond to their customers quickly, confidently, and accurately.
(click to expand)
My goal was to meet three standards:
(1) The application should be usable from any device. Sales calls often come when you're not at your desk, and finding what you need should be as easy as if you were.
(2) The UI should be as clear a window to the information as possible. When the phone rings and you focus the tab, the search box receives focus. Typing any keyword starts opening the best matched orders. Dependencies are laid out in blocks, and their states in a high-constrast tree, so visual recognition can lead the way.
(3) The presentation and interaction should be a direct mapping of our daily process, in what signals we send and what details we need. I believe that if highly visual data is placed in front of us in the right way, that resource can become an unconscious extension of our planning and decision making.
The first iteration of PartCenter was entirely focused on the parts. The first code I wrote used a QR scanner to identify part numbers from bin labels; depending on the type of part it would then present a visual or exact count entry.
Items were grouped based on turnover and alerts were shown demanding counts for overdue items. Opening the QR scanner presented entries from these lists.
This was the most important aspect of the project to me, but PartCenter became too time intensive and I had to set it aside.
3913 lines of TypeScript and 4027 lines of C#
Our bins have slots in the front so I made PETG tags to fit. I found labels for an extra labeler that fit well, so I designed the physical part of the system around those. The goal here was to get the best alignment possible while being easy to do hundreds of times.
I iterated on FDM parameters until the tags were almost impossible to break under normal (ab)use.
Hobbies
I had access to AC TIG machines in our partner's shop and I got super into it for a while.
I learned mostly from
6061.com,
the wonderful Mr. TIG at the
Weld.com YouTube channel,
and an assortment of metallurgy literature.
It turns out this is really difficult! My first welds on stainless turned out about how you'd expect.
I really enjoyed welding aluminum. When I set up a new shipping room in our warehouse I was able to make much better use of the space by building out aluminum fixtures for the equipment.
My first real welding project was tool cart (in A513) that I could tear down to fit in my car.
I also learned to use the plasma cutter when I forgot to leave access to some bolts :)
After welding it was only 1/16" out of square front to back, which actually helped to snug up the toolbox.
I've been asked about the tool holders, which I highly recommend. They're screwed into rivnuts (recommended setter) and spaced with a nut behind them to set the tightness.
iRacing, simply the best online competitive racing experience you can bring home. Carbon fiber seat on sliders and telescoping steering column, fits drivers from 5' to 6'5. Three pedals with paddle and H-pattern shifting. Annie's driving the twin turbo V8
McLaren MP4-12C in the GT3 class.
With a removable
HOTAS addon, and the clutch and gas as rudder pedals, the rig plays double duty as a cockpit for my favorite flight simulator,
DCS. A while ago I got it set up with Oculus Rift and it brought back all the excitement and adventure of playing flight sims as a kid.
I have some resources for setting up DCS
here.
I spent the last year in the
F/A-18C; specifically a simulation of the U.S. Navy's
BuNo 165407 from lot 20—one of the last legacy Hornets (built in 1998, with electronics upgrades from 2005).
As of January 2019 this particular aircraft (pictured here) is stationed in
Miramar, CA.
I just started learning the
UH-1 Huey, but I still fly the Hornet as much as possible.
West Clear Creek, AZ
Highway 87, AZ
'99 BMW R1100RS - Oil-cooled flat twin with shaft drive and Telelever suspension
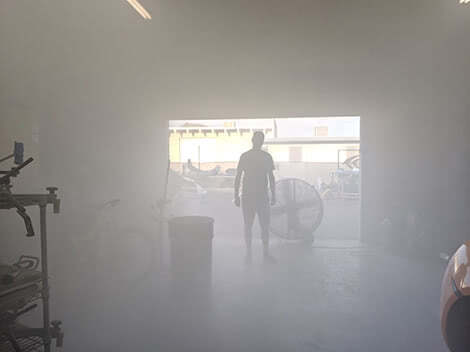
We're full-time problem solvers :)